The ABC of the correct use of power generators
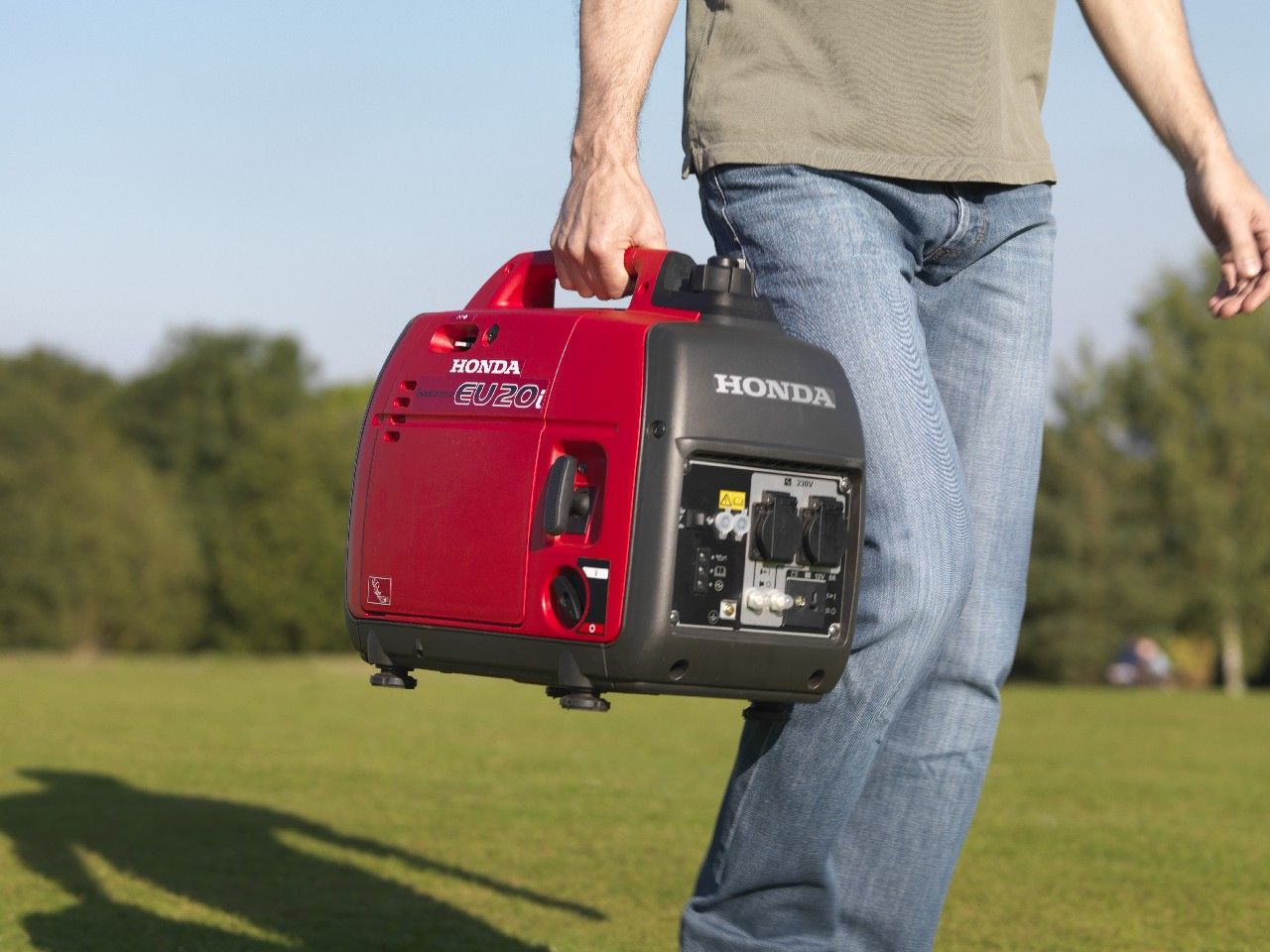
Generator sets are, as a rule, intended for many years of use and will serve for a long period, provided that they are of original production, are properly used and properly maintained - in accordance with the manufacturer's recommendations contained in the operating manual. It is worth remembering that a properly functioning power generator also has a significant impact on the functioning, durability and life of the supplied receivers.
Correct operation of the aggregate applies to both its use, maintenance and storage. The unit, like any device, is equipped with consumables that naturally wear out during operation - and the greater the intensity of use of the device, the faster these parts wear out.
The expert advises
"Systematic inspections of devices, and above all of those parts whose technical condition affects the proper functioning of a given device, are extremely important and necessary. Basic instructions for inspection and maintenance of the generator and its consumables are provided in the operating instructions. Of course, the recommended timescales are based on standard parameters of time and intensity of use. So you have to remember that if the generator is used intensively, often and for a long time, it should be checked more often. " - says Wojciech Zawada, Manager of the Spare Parts and Accessories Department at Aries Power Equipment, which is the General Distributor of Honda machines and devices in Poland.
The basic scope of maintenance for power generators is the same as for all devices equipped with an internal combustion engine. All negligence in this regard, even the most trivial ones, may ultimately lead to damage to the working component, the engine and even the entire device. Then the repair costs can also be high.
The most "sensitive" elements of each machine are the so-called consumables that wear naturally during use. These are, for example, depending on the type of machine: filters, spark plugs, steering / steering cables and rods, rubber and rubber-metal elements, seals, fuses for power equipment, etc. Regular inspections of their technical condition and replacement are necessary due to the impact of are for the proper functioning of the machine. The most important factors for the durability of the device are air and fuel filters.
Basic principles of the correct operation of the aggregate:
- the first step is the correct selection of the generator and the correct connection of the receivers - the basic rule is to determine the active power of the aggregate, which should be greater than the total power of the receivers that will be connected to it at the same time, and increased by the value of the power required when starting the receivers. This extra power comes from the so-called inrush currents that appear in all electrical consumers. The starting currents vary from one load to another, so it is advisable to consult an authorized generator dealer to determine the generator power.
- getting acquainted with the instruction manual of a given model , which contains information, among others on the operation of the device, maintenance and the recommended frequency of technical inspections,
- checking the setting of the chiller before starting - this activity applies mainly to portable aggregates used in various places. In such cases, make sure that the device is placed on a flat, even surface,
- oil level check - checking the oil level is recommended before each start of the unit. If necessary, refill the reservoir to the top of the filler neck. Each manual contains information about the recommended oil for a given type of engine,
- fuel level control - the amount of fuel must not be allowed to fall below the minimum level. The fuel cap should be tightened each time after refueling. It is also worth remembering not to leave fuel in the tank, because if left for more than a month, it loses its properties, and sediment forms in the tank, which then goes to the carburetor and clogs its nozzles. The nozzles, on the other hand, are sensitive to the smallest sediment particles and are clogged, preventing the engine from starting. These effects can be prevented by not keeping fuel in the tank and by regularly changing the filter. If you suspect that the carburetor nozzles are clogged, you must necessarily deliver the machine to an authorized service center,
- air filter control - the air filter is subject to natural mechanical wear, therefore it should be regularly cleaned and replaced at least once a year. Clogged, it restricts the flow of clean air the engine needs to operate properly.
“The consequences of not getting enough clean air to the engine are serious. Generally speaking, this lowers its power, worsens performance and increases fuel consumption. It is also necessary to add here the excessive emission of exhaust gases entering the environment, higher operating costs and much louder engine operation. I would also like to emphasize very strongly that the internal combustion engine cannot work without a dedicated air filter, otherwise the engine will go to the site sooner rather than later. " - explains Wojciech Zawada
A damaged air filter allows dust and sediment to pass through the carburetor, which leads to excessive and rapid wear of the engine cylinders, pistons and rings. A worn or damaged air filter reduces engine power, worsens machine performance, and increases fuel consumption. It also affects the environment, because its poor condition results in excessive exhaust emissions,
- checking the condition of receivers - before connecting the receivers to the generator, check whether they are operational.
We have created the CampRest portal for people who value freedom and travel on their own.